
CFD Modeling
Computational fluid dynamic (CFD) modeling is an advanced simulation technology which is capable of performing detailed combustion analysis of burners to study the flow temperature profiles along with the flue gas circulation pattern in the heater. The simulation helps to understand the heater insights in terms of flue gas flow pattern, heat flux distribution over radiant tubes, tube metal temperatures, and temperature distribution in the heater.
At Furnace Improvements, we utilize CFD to study design and operating conditions of heaters, locate problems and provide solutions:
- Evaluate burner configurations, to improve heater performance
- Uniform air flow distribution across all burners
- Design of Ammonia Injection Grid to have uniform mixing
- Uniform process fluid distribution across transfer lines
- Reduce system pressure losses for ID fan suction and discharge side
This tool enables us to study the existing design and operating conditions of heaters and determine recommendations for solving any difficulties. CFD gives a competitive edge over other analyses due to its visual presentation of the observed conditions and proposed modification.
Case Study 5: Reducing System Pressure Losses for ID Fan
Sudden sharp 90o bends at inlet and outlet of ID Fan causes high pressure losses which in turn reduces the overall capacity of the heater or demands for a higher rating fan. CFD simulations provide insight of the flow profile and region of high and low velocity region causing most of the pressure drop in the system.
Installing turning vanes and minor modifications to the inlet duct of ID Fan, uniform flow distribution was achieved at the inlet and pressure drop was reduced by 0.5 inches w.c.
On the ID Fan discharge side, the flow come out through the fan outlet with a typical flow profile, which has higher air velocity in the top and lower velocities in the bottom region. Baffles are installed in the inlet duct upstream of the bend in addition to the turning vanes in the bend to improve the flow distribution and reduce the system pressure losses. A reduction of about 0.5 inches w.c. was obtained by making minor modifications to the duct and installing turning vanes in the stack.
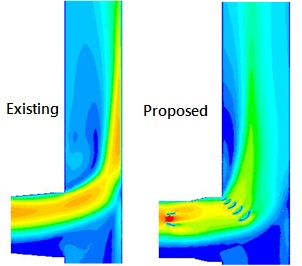